BEYOND | pavilion of innovation 2015
EXHIBITION | responsive environments
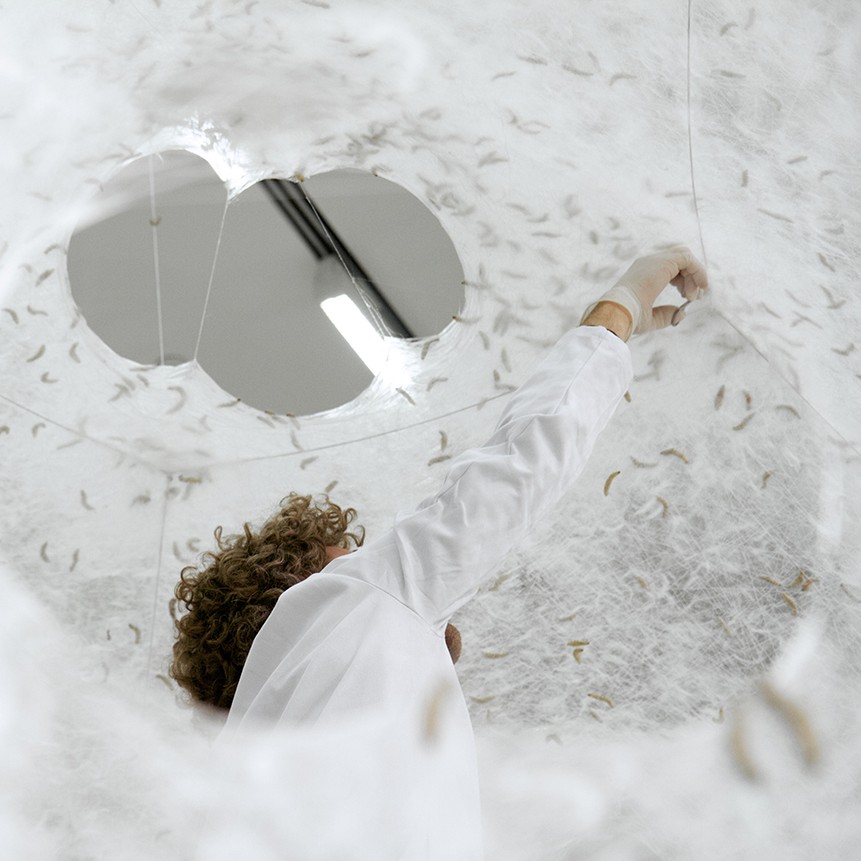
Silk Pavilion; by Mediated Matter Group, MIT Media Lab, United States of America
The Silk Pavilion explores the relationship between digital and biological fabrication on product and architectural scales.The primary structure was created of 26 polygonal panels made of silk threads laid down by a CNC (Computer-Numerically Controlled) machine. Inspired by the silkworm’s ability to generate a 3D cocoon out of a single multi-property silk thread (1km in length), the overall geometry of the pavilion was created using an algorithm that assigns a single continuous thread across patches providing various degrees of density. Parallel basic research explored the use of silkworms as entities that can “compute” material organization based on external performance criteria. Specifically, we explored the formation of non-woven fiber structures generated by the silkworms as a computational schema for determining shape and material optimization of fiber-based surface structures. Research and Design by the Mediated Matter Research Group at the MIT Media Lab in collaboration with Prof. Fiorenzo Omenetto (TUFTS University) and Dr. James Weaver (WYSS Institute, Harvard University).
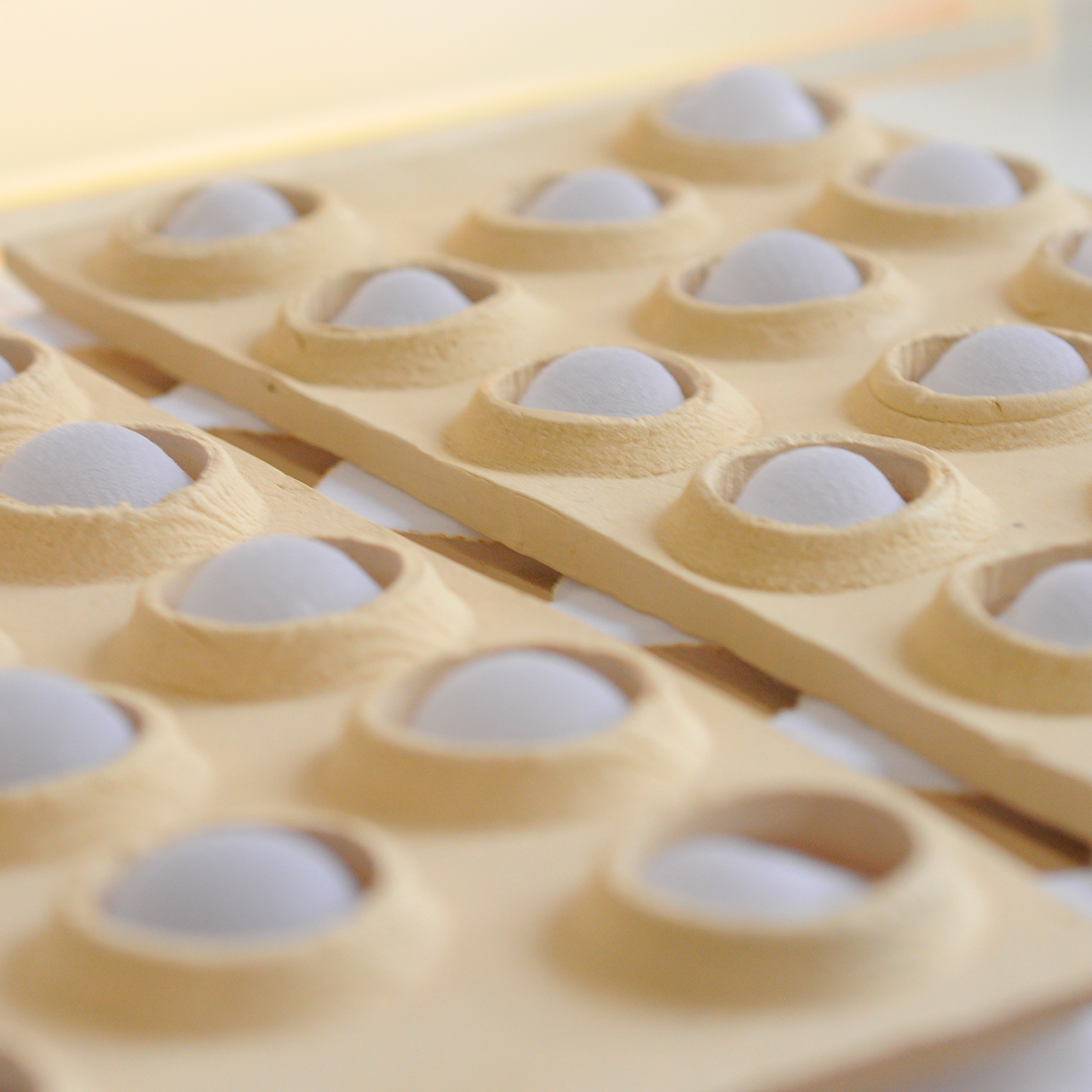
Hydroceramic; DMIC studio, Institute for Advance Architecture of Catalonia (IAAC), Spain
Team Members: Akanksha Rathee, Pong Santayanon, Elena Mitrofanova
The studio [DMIC] DIGITAL MATTER INTELLIGENT CONSTRUCTIONS in the academic year 2014 at IAAC aimed to redefine and embed ‘intelligence’ into the built environment by the use of responsive materials, designing and implementing systems to aid the building performance by digital simulations and fabrication. This project aims to speculate the thermodynamic processes in a building and how these can be tackled passively with a class of materials called ‘hydrogel’. The term ‘hydrogel’ refers to a class of substances that absorb and retain 500 times their weight in water.Chemically they can be insoluble polymers of hydroxyethyl acrylate, acrylamide, polyethylene oxide, and others. As a cooling aid they work by exposing the absorbed water to a large surface area. Since the heat of vaporization of water is about 0.6 kilocalories per gram, a cooling effect occurs. Taking this phenomenon as a hypothesis, the project aims at prototyping a custom building element by the hygothermal analysis of buildings to meet the habitable conditions required for the comfort zone in a particular context.
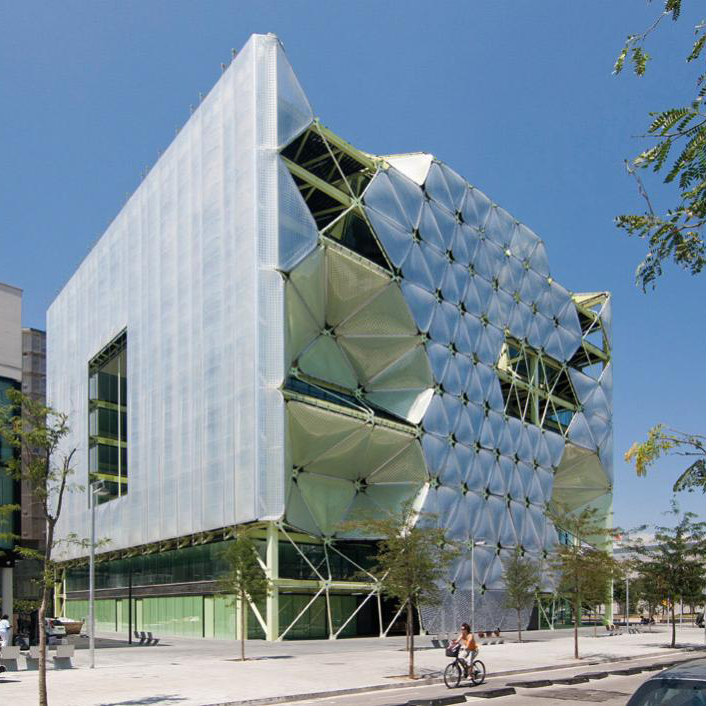
Media TIC; by Cloud 9, Spain
This building seeks to be iconic in the digital world and a vehicle for the dissemination of new technologies, while being designed as a socially open civic space. The building is in the shape of a cube and formed by large iron beams covered in a plastic coating of inflatable bubbles, which offer glimpses of the fluorescent structure of the building. The attractive covering also has a functional utility as a way of regulating light and temperature, primarily preventing 114 tons of CO2 a year from escaping from the building, and offering a 20% saving on climate control. Every facade of the Media-TIC is different: from the outside, they reveal parts of their interior spaces and give a diverse plasticity, while from the inside they offer spectacular views. The translucent and innovative covering, ETFE (Ethylene Tetrafluor Ethylene), recently approved as a construction material, is in itself an innovation in Spanish building: it acts as an external covering and a mobile sunscreen that helps light to penetrate and affords heat savings. The ETFE skin is activated using pneumatic mechanisms thanks to “luxometer” sensors that automatically and independently activate the chamber inflation and deflation devices according to how much solar energy is there.
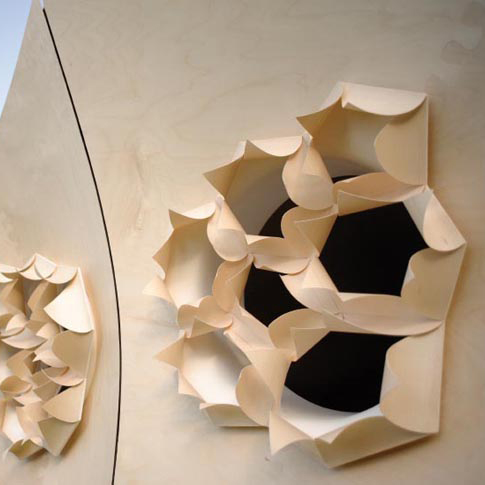
HygroSkin – Meteorosensitive pavilion; ICD Universität Stuttgart, Germany
The project HygroSkin – Meteorosensitive Pavilion explores a novel mode of climate-responsive architecture. While most attempts towards environmental responsiveness heavily rely on elaborate technical equipment superimposed on otherwise inert material constructs, this project uses the responsive capacity of the material itself. The dimensional instability of wood in relation to moisture content is employed to construct a metereosensitive architectural skin that autonomously opens and closes in response to weather changes but neither requires the supply of operational energy nor any kind of mechanical or electronic control. Here, the material structure itself is the machine.
The project was commissioned by the FRAC Centre Orleans for its renowned permanent collection and will be first shown in the exhibition ArchiLab 2013 – Naturalizing Architectureopening on 14th of September 2013.
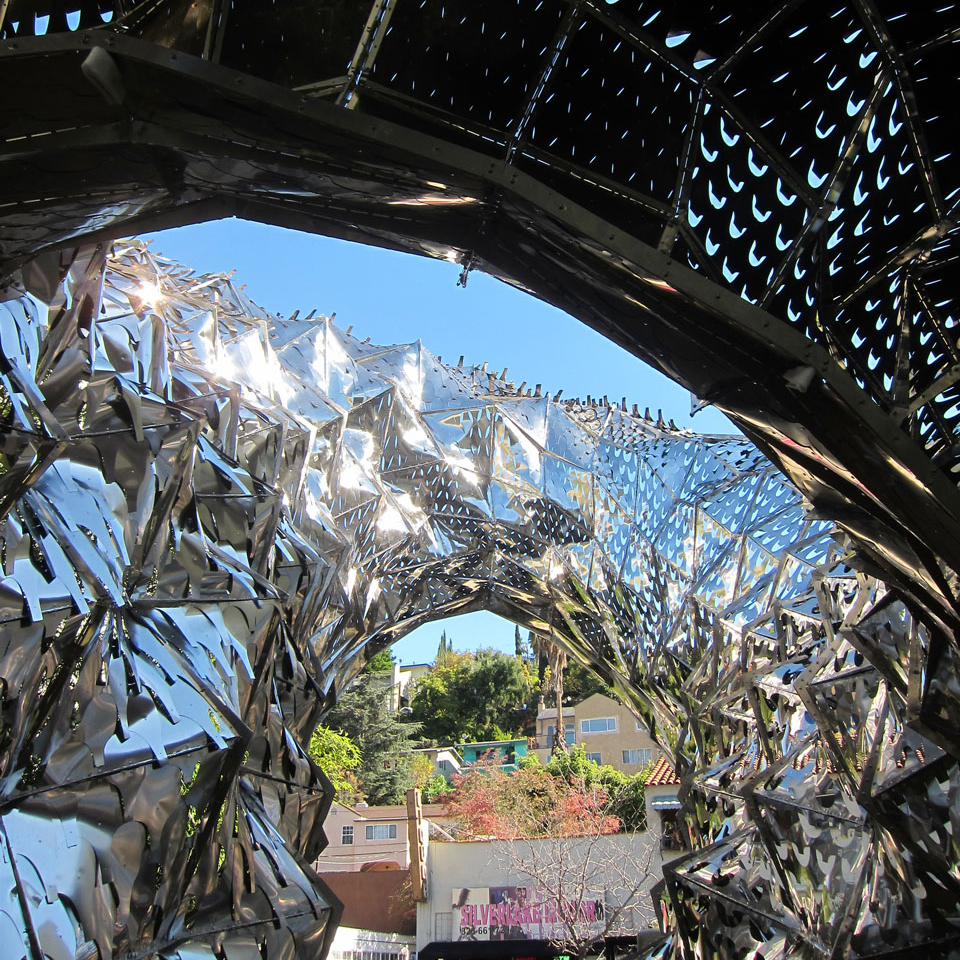
Bloom; by Do|Su Studio Architecture, United States of America
A sun-tracking instrument indexing time and temperature, “Bloom” stitches together material experimentation, structural innovation, and computational form/patternmaking into an environmentally responsive installation. The form’s responsive surface is made primarily out of 14,000 smart thermobimetal tiles, where no two pieces are alike. Each individual piece automatically curls a specified amount when the outdoor ambient temperature rises above 70F or when the sun penetrates the surface.
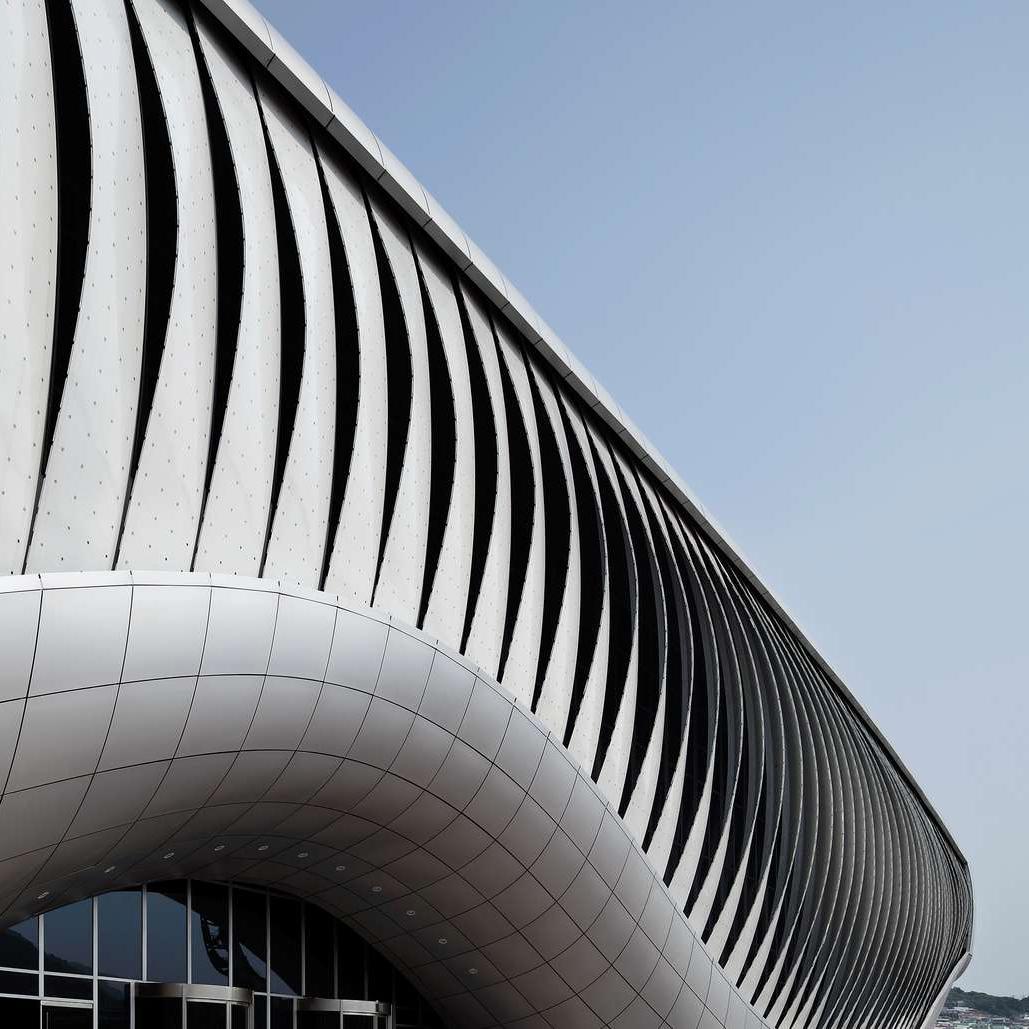
Theme Pavilion expo 2012; by SOMA Architecture, Austria
As a major and permanent facility the Thematic Pavilion embodies the Expo’s theme “The Living Ocean and Coast” in manifold ways. The aim of the design is to create an iconic landmark that is integrated into its urban context and the surrounding nature. We experience the Ocean mainly in two ways, as an endless surface and – in an immersed perspective – as depth. This plain/profound duality of the Ocean motivates the building’s spatial and organisational concept. Continuous surfaces twist from vertical to horizontal orientation and define the significant interior spaces. The vertical cones induce the visitor to immerse into the Thematic Exhibition. They evolve into horizontal levels that cover the foyer and become a flexible stage for the „Best Practice Area“. Continuous transitions between contrasting experiences also form the outer appearance of the Pavilion. Towards the sea the conglomeration of solid vertical cones defines a new meandering coast line, a soft edge that is in constant negotiation between water and land. Opposite side the pavilion develops out of the ground into an artificial roof–landscape with gardens and scenic paths. The topographic lines of the roof turn into lamellas of the kinetic media façade that faces the Expo’s entrance and the “Digital Gallery”.
EXHIBITION | rapid prototyping
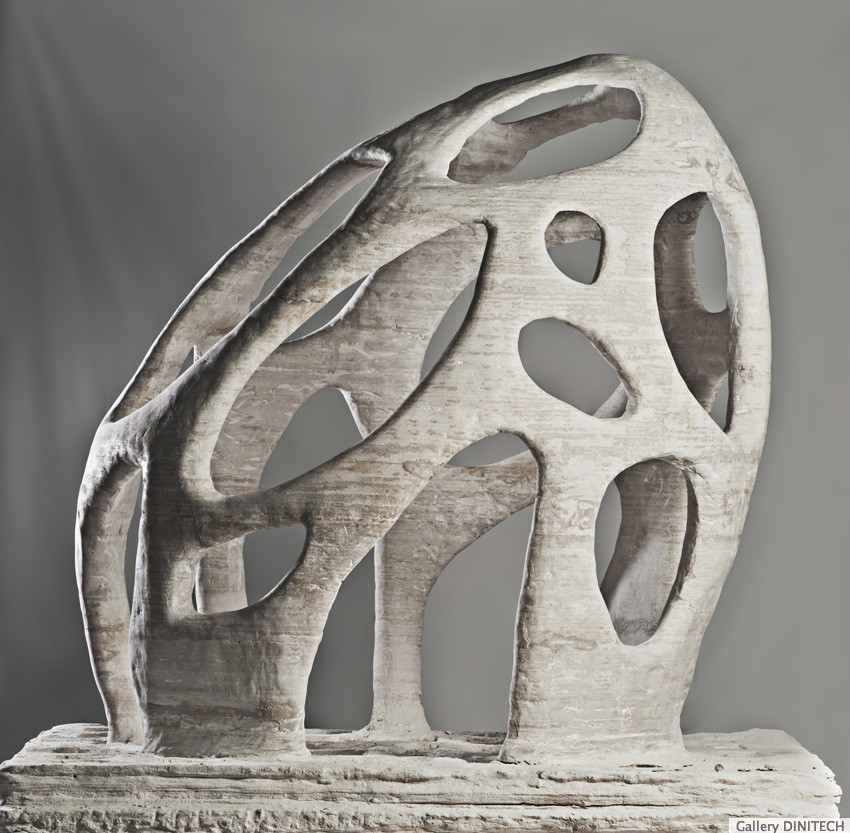
D-shape by Enrico Dini, Italy
D-Shape is a new robotic building system using new materials to create superior stone-like structures. This new machinery enables full-size sandstone buildings to be made without human intervention, using a stereolithography 3-D printing process that requires only sand and our special inorganic binder to operate. D-Shape is a new building technology which will revolutionize the way architectural design is planned, and building constructions are executed. By simply pressing the “enter” key on the keypad we intend to give the architect the possibility to make buildings directly, without intermediaries who can add interpretation and realization mistakes.
Today’s Construction technology lags behind the available Computer Design Technology. The new 3D CAD software allow architects to conceive and design constructions easily, but existing building methods do not allow the full potential of the new design software to be achieved.
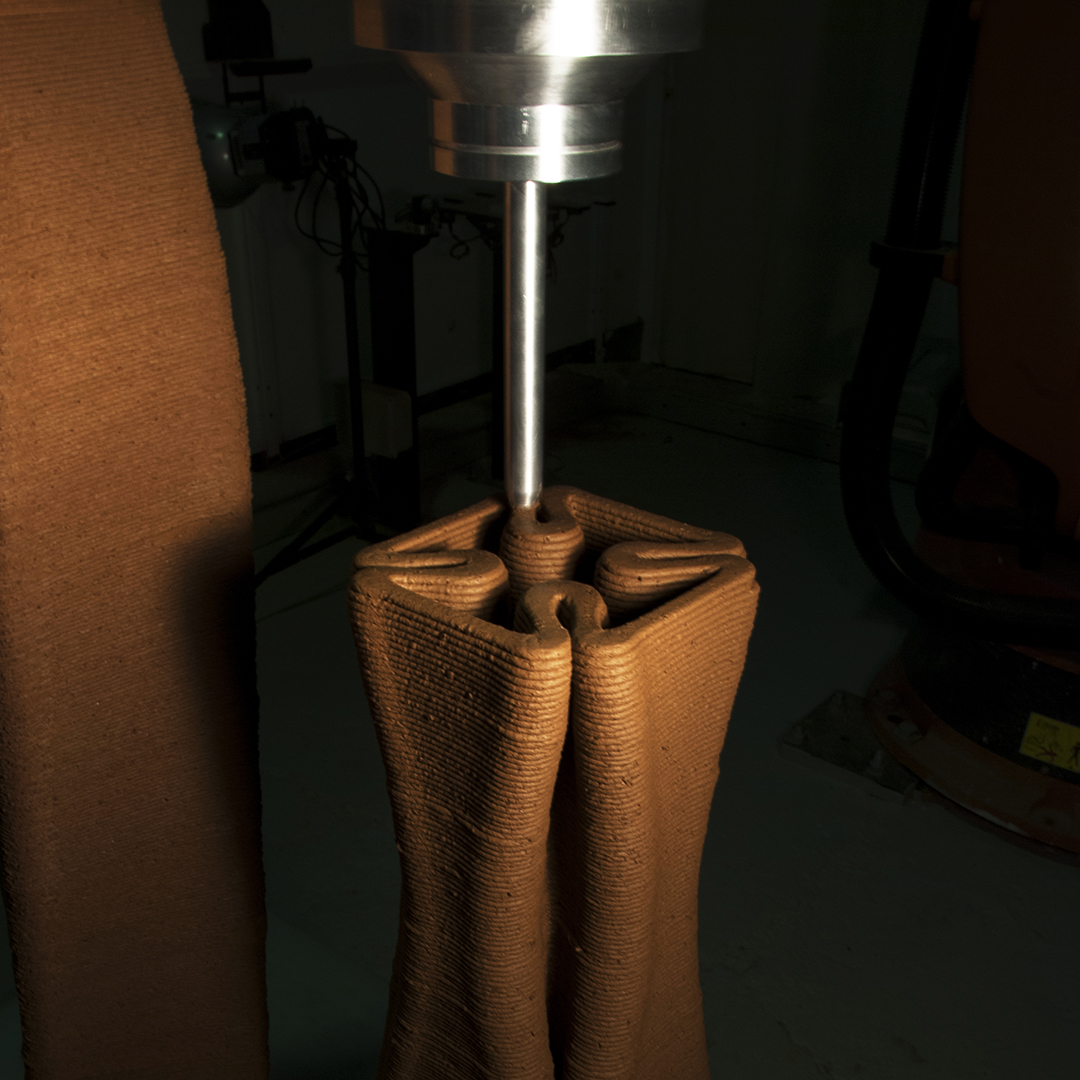
Pylos; OTF Studio, Institute for Advance Architecture of Catalonia (IAAC), Spain
Team Member: Sofoklis Giannakopoulos
This abstract portrays the interest to develop printing as a construction method, moreover when printing with natural, biodegradable, recyclable and locally found materials, particularly in this time of economic and environmental crisis, is undeniable. This material can not be other than soil. Project is focusing to the natural properties of soil. Earth, or Soil, as a construction material has been used since Neolithic times. The advantages of an earth – soil structure are primarily related to both environment and economy, being secure and friendly to our environment. Soil also offer the benefits of natural insulation, fire protection, air circulation, low first cost, 100% recyclable structures, stiffness, great strength, thermal flywheel effect, low green house emissions, regulator of the climate, providing a healthy Indoor environment and a lot more. The material results obtained through the development of the first phase of this research project are extremely promising reviling an new, more than 96% based in soil, material that has 3 times higher tensile strength from industrial hard clay. The project as well got inspiration from one of unbaked soil properties.

Mini Builders; OTF Studio, Institute for Advance Architecture of Catalonia (IAAC), Spain
Team Members: Stuart Maggs, Dori Sadan, Shihui Jin, Saša Joki?, Petr Novikov
There has always been a close relationship between the advances in technology and the further development of architecture. However, in more recent times, architecture has stagnated and the construction industry has been slow to adopt technologies that are already well established in other fields, as is the case with the application of robotics. The objective was to develop a family of small scale construction robots, all mobile and capable of constructing objects far larger than the robot itself. Moreover, each of the robots developed was to perform a diverse task, linked to the different phases of construction, finally working together as a family towards the implementation of a single structural outcome. Hence, instead of the implementation of one large machine, a number of much smaller robots were generate, working independently, but in coordination, towards a single goal. Specifically, a family of three robots was developed, each robot linked to sensors and a local positioning system. These feed live data into a custom software allowing to control the robots’ movement and deposition of the material output: fast setting artificial marble.
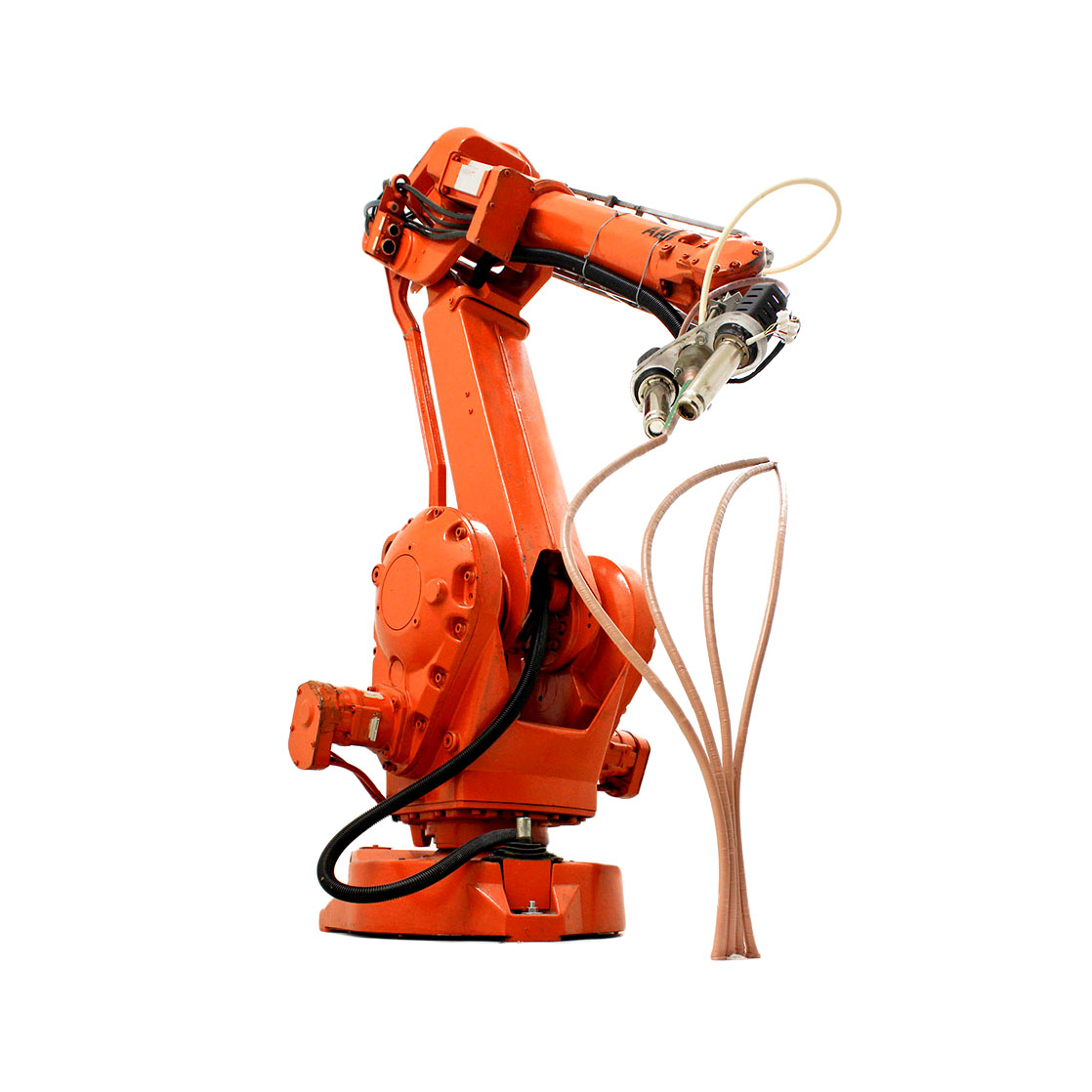
Mataerial; OTF Studio, Institute for Advance Architecture of Catalonia (IAAC), Spain
Team Members: Petr Novikov, Saša Joki?, Joris Laarman Studio
MATAERIAL – a brand new method of additive manufacturing. This patent-pending method allows for creating 3D objects on any given working surface independently of its inclination and smoothness, and without a need of additional support structures. Conventional methods of additive manufacturing have been affected both by gravity and printing environment: creation of 3D objects on irregular, or non-horizontal surfaces has so far been treated as impossible . By using innovative extrusion technology we are now able to neutralize the effect of gravity during the course of the printing process. This method gives us a flexibility to create truly natural objects by making 3D curves instead of 2D layers. Unlike 2D layers that are ignorant to the structure of the object, the 3D curves can follow exact stress lines of a custom shape. Finally, our new out of the box printing method can help manufacture structures of almost any size and shape.
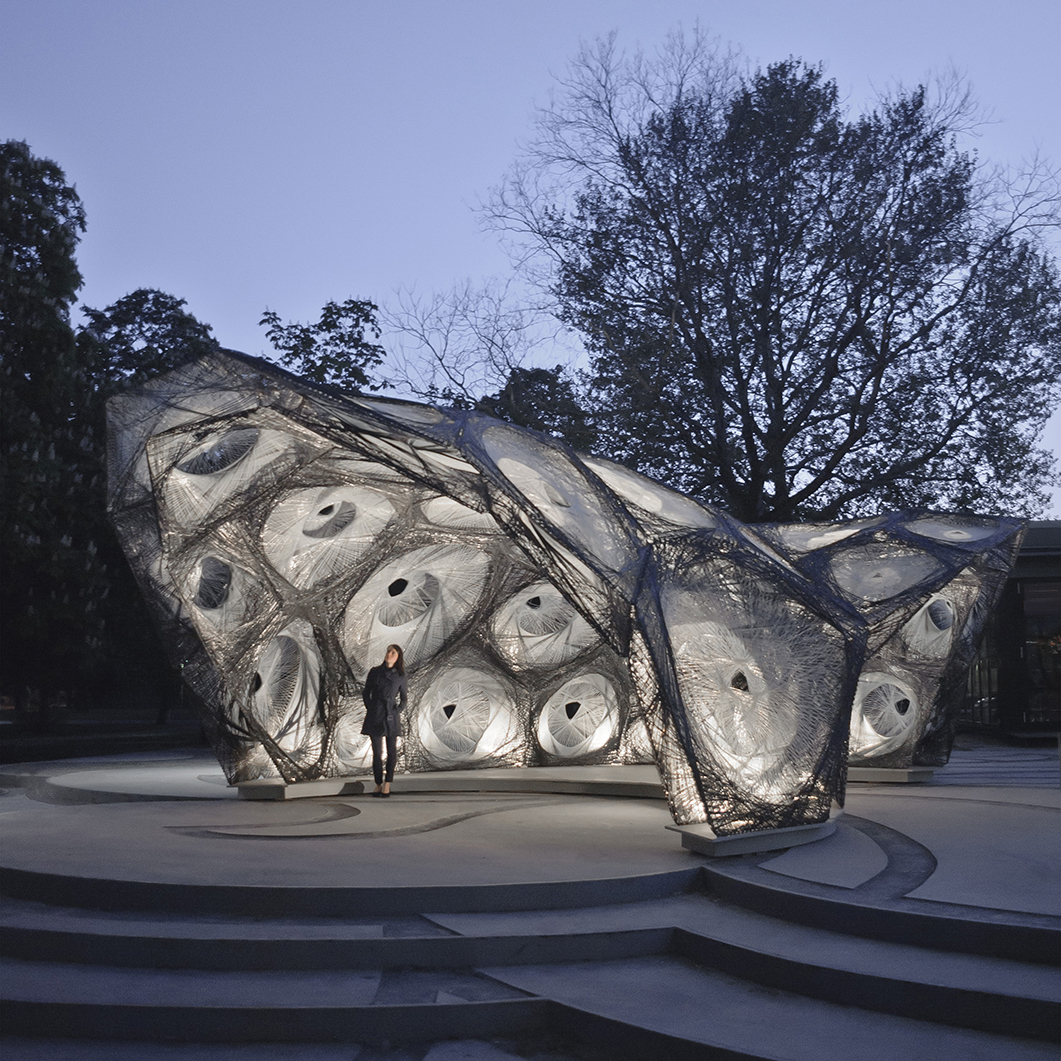
ICD/ITKE Research Pavilion 13-14; by Institute for Computational Design (ICD) – Prof. Achim Menges, Institute of Building Structures and Structural Design (ITKE) – Prof. Jan Knippers, Germany
The focus of the project is a parallel bottom-up design strategy for the biomimetic investigation of natural fiber composite shells and the development of novel robotic fabrication methods for fiber reinforced polymer structures. The aim was the development of a winding technique for modular, double layered fiber composite structures, which reduces the required formwork to a minimum while maintaining a large degree of geometric freedom. Therefore, functional principles of natural lightweight structures were analyzed and abstracted in cooperation with researchers on evolution and ecology and paleobiology. Through the development of a custom robotic fabrication method, these principles were transferred into a modular prototype pavilion.
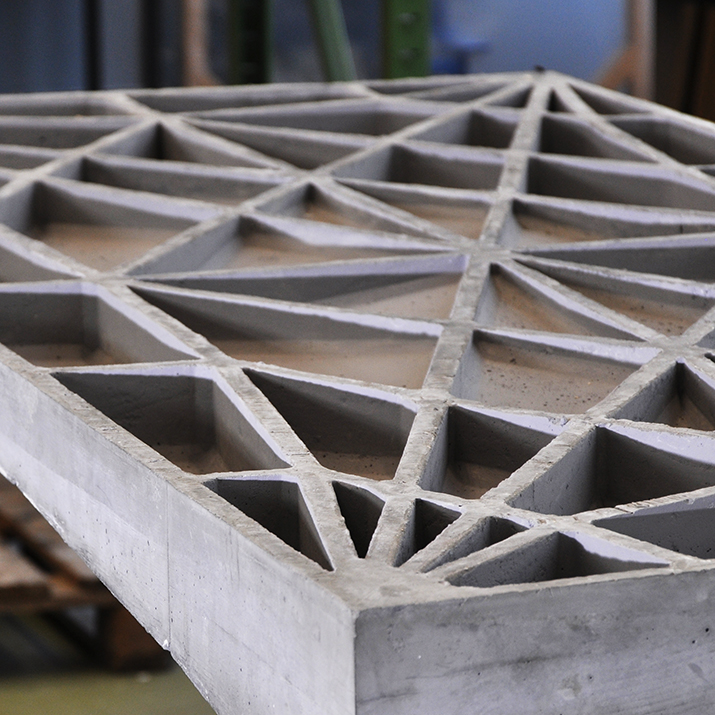
Integrated Funicular Floor; by BLOCK Research Group, ETH Zurich, Switzerland
Introducing funicular vaulting as a floor system results in an extremely lightweight floor system with savings of more than 70% of weight compared to traditional concrete floor slabs. This also allows for a natural and efficient integration of services and low energy heating – and cooling systems, further saving significant floor height (BRG, SuAT). The system is of a bespoke, modular and prefab nature, made possible through a robotically controlled, intelligent fabrication setup, resulting in lightweight elements that can very quickly be assembled on site (sM).
EXHIBITION | novel & smart materials
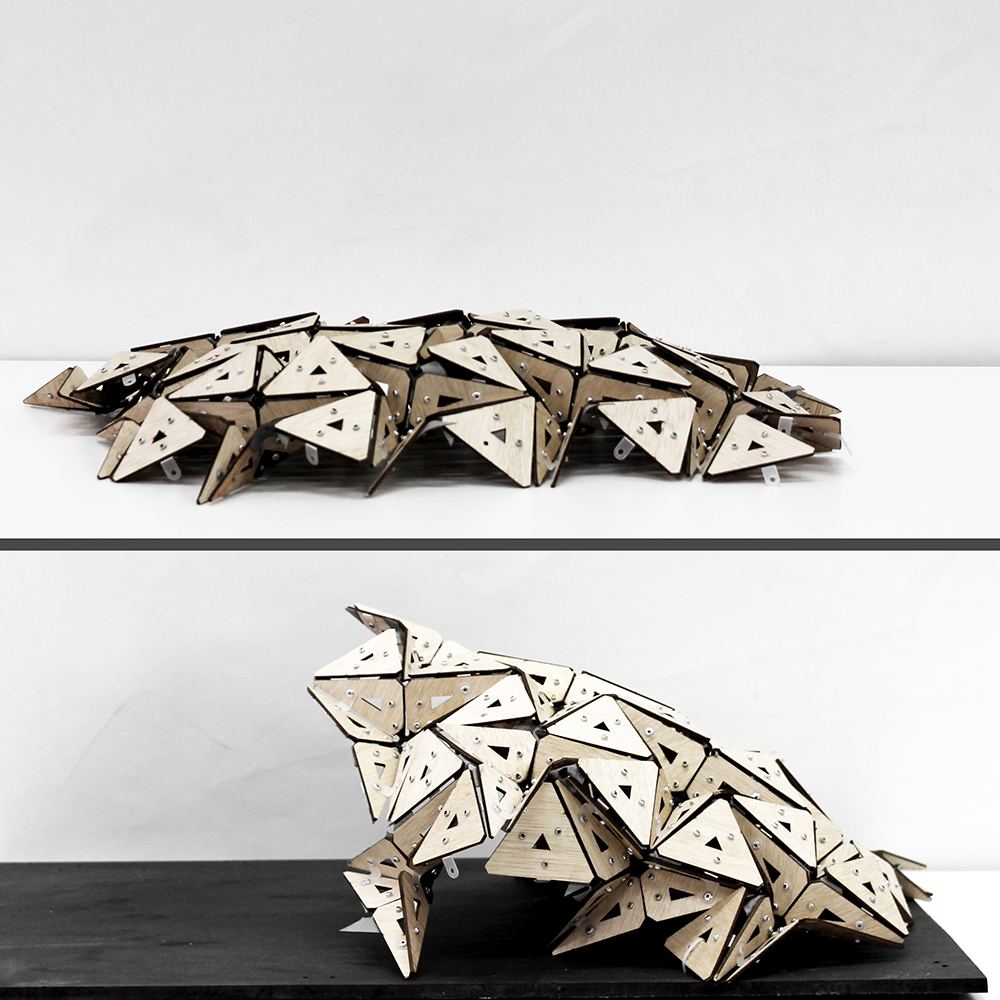
Translated Geometries; DMIC studio, Institute for Advance Architecture of Catalonia (IAAC)
Team Members: Efilena Baseta, Ece Tankal, Ramin Shambayati
We propose an architecture of transition. A series of transitions between forces, (material) phases, people, spaces, and functions. Form does not always follow the functions that we cannot predict but rather the phases that our new built environments can go through in their relationship with humans, nature, and existing buildings. Having said this, we cannot expect changes in our spaces and structures if the fundamental basis of architectural construction, the material, is still viewed as a sedentary element in our systems. A thorough understanding of smart materials and properties suitable for an adaptable architecture is therefore essential in gaining an understanding of their countless possibilities and limitations. In our studio project we have been working with Shape Memory Polymer (SMP) in order to apply it to a responsive architectural prototype. As our concept was based around the motif of architecture in transition, are using a material that can change phase from an external and controlled stimuli.
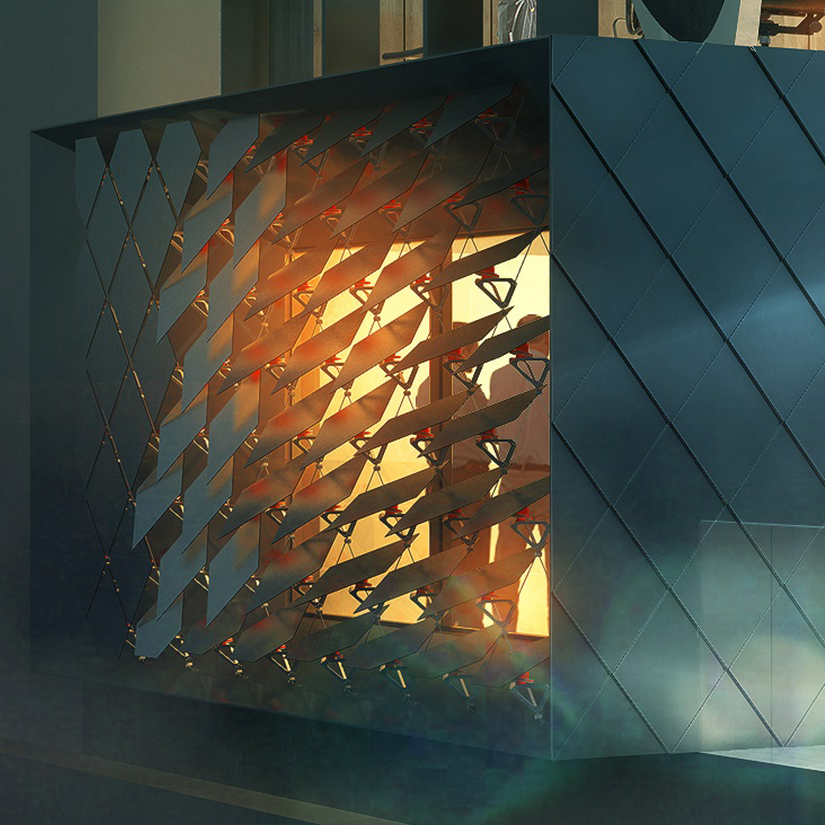
Adaptive Solar Facade; A/S – Architecture and Building Systems; ETH Zürich, Switzerland
The Adaptive Solar Facade (ASF) is a dynamic facade of thin film photovoltaic modules with soft pneumatic actuators for solar tracking and daylight control. The elements provide solar energy generation, shading and control the visibility and transparency of the façade. The elements can rotate to respond to changes of the outside environment and the demands of the interior occupant. The different modes of the modules are controlled based on sensor as well as on occupant input. Adaptive learning algorithms facilitate the continuous improvement of the behaviour and thus the adaption of the modules to their users and environments (SuAT).
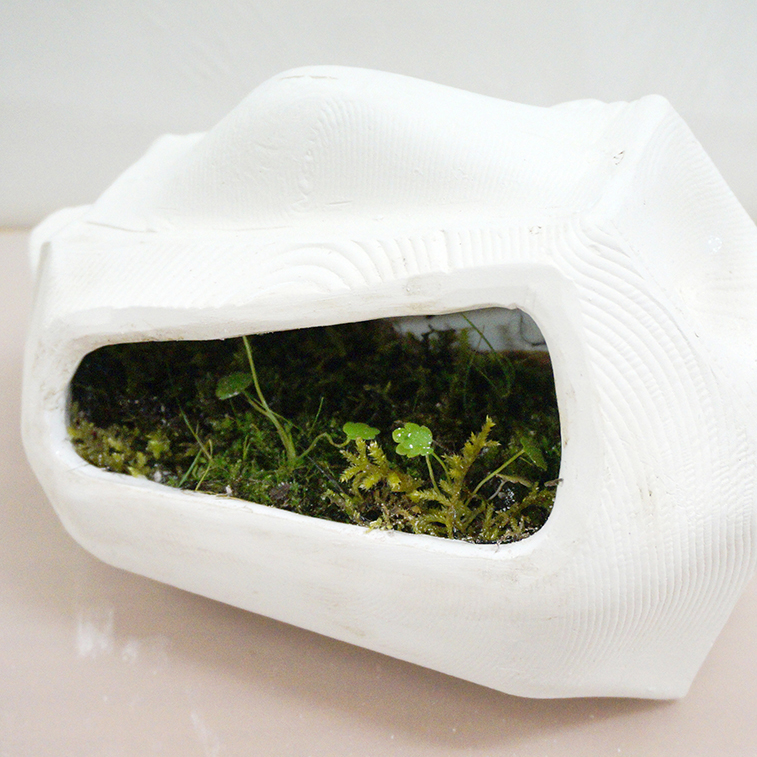
Moss Voltaics; OTF Studio, Institute for Advance Architecture of Catalonia (IAAC), Spain
Team Member: Elena Mitrofanova
This project is the exploration how moss could be used as a source of renewable energy. Mentioned emerging technology is called biophotovoltaics (BPV) which uses the natural process of photosynthesis to generate electrical energy. Photosynthesis is a process by which plants and algae convert carbon dioxide from the atmosphere into organic compounds using energy from sunlight. The plants use these organic compounds (like carbohydrates, proteins and lipids) to grow. When the moss photosynthesises it releases some of these organic compounds into the soil, which contains bacteria. The bacteria break down these organic compounds, which they need to survive, liberating by-products that include electrons. By providing an electrode for the micro-organisms to donate their electrons to, the electrons can be harvested as electricity. These electrons are captured by conductive fibers inside the prototype.
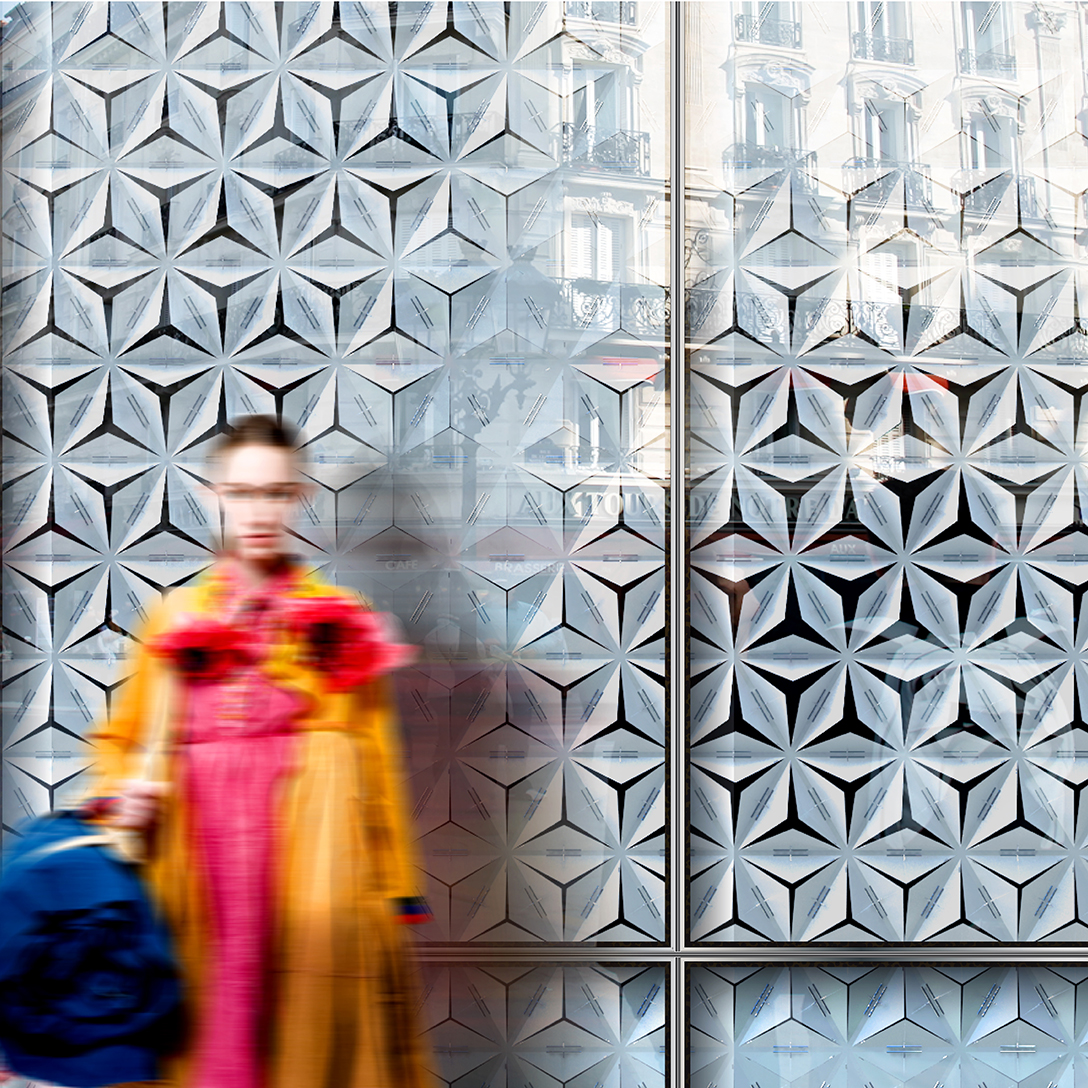
Pixel Skin; by Sachin Anshuman, Orangevoid
Developed by Sachin Anshuman, Principal Organizer for the Intelligent Building Laboratory at GCU Glasgow and creator of Orange Void, Pixel Skin is a smart surface designed to regulate light, solar radiation and views, as well as display dynamic signage. Anshuman’s prototype uses shape memory alloys (SMA) to actuate each of four triangular panels residing within a single module, and each surface acts as a “pixel” with 255 increments between open and closed states. Pixel Skin is designed to create dynamic windows which allow views or control internal lighting conditions across the building membrane in response to particular subject states and their positions. The surface may also simultaneously be used to generate low resolution images, low refresh-rate videos, or abstract patterns. A response to common conflicts encountered with daylighting and signage in contemporary architectural surfaces, Pixel Skin is an electrographic surface which allows the integration of illumination and view controls with real-time communications media.
EXHIBITION | distributed manufacturing
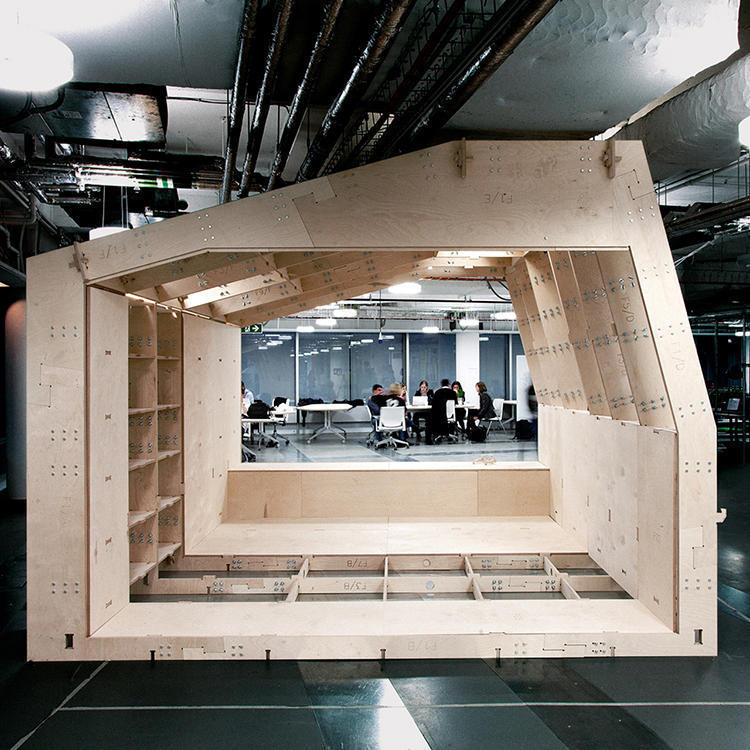
WikiHouse; by Alastair Parvin, United Kingdom
WikiHouse is an open-source project for designing and building houses. It endeavours to democratise and simplify the construction of sustainable, resource-light dwellings. The project was initiated in the summer of 2011 by Alastair Parvin and Nick Ierodiaconou of 00, a London based strategy and design practice, in collaboration with Tav of Espians, James Arthur now with 00 and Steve Fisher of Momentum Engineering. It was launched at the Gwangju Design Biennale in Gwangju, South Korea. The project has since grown to include many chapters around the world. WikiHouse enables users to download Creative Commons-licensed building plans from its website, customize them using SketchUp, and then use them to create jigsaw puzzle-like pieces out of plywood with a CNC router. Construction of WikiHouse structures requires no special parts because the cut pieces of wood snap together with wedge and peg connections inspired by classical Korean architecture. The frame of a WikiHouse can be assembled in less than a day by people with no formal training in construction. The frame must then be finished with cladding, insulation, wiring and plumbing before it can be inhabited.
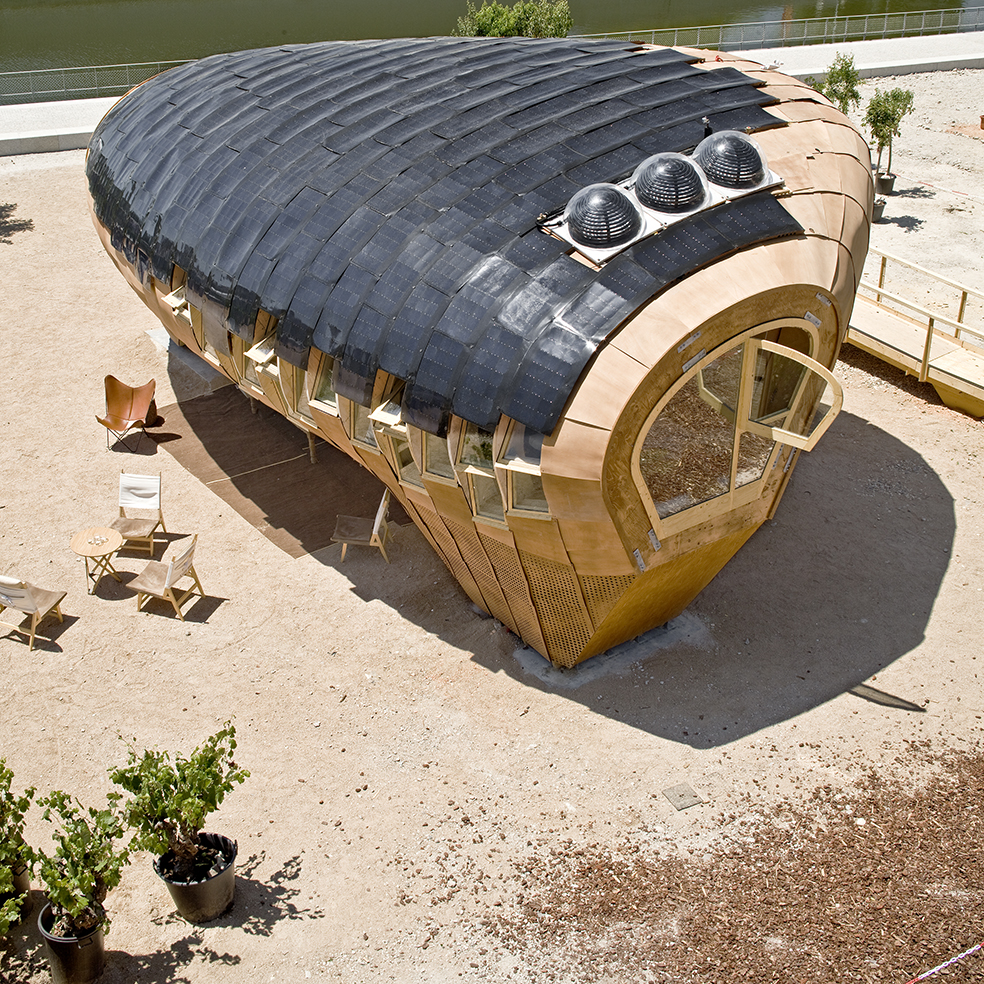
FabLab House; by Institute for Advance Architecture of Catalonia (IAAC), Spain
The project, which involved architects and experts from 20 countries, is being developed by the Institute for Advanced Architecture of Catalonia (IAAC), The Center for Bits and Atoms from the Massachusetts Institute of Technology (MIT) and the worldwide network of Fab Labs. The project was carried out with the collaboration of a large group of companies, led by Endesa, Schneider Electric, Visoren, Roca, Santa & Cole, Vinçon and Nani Marquina.The main structure of the house has been fabricated in Germany with large scale CNC Machine, the remaining components of the house such as interior, skin and other elements have been fabricated in the Fab Lab Barcelona. The Fab Lab House is much more than a house fabricated with CNC Machines, is the result of a team work with people coming from 25 different countries. One team, on project. The Fab Lab House wins Solar Decathlon Europe people’s choice award. More than 20,000 people have visited the most popular solar house in Madrid, produced by the Institute for Advanced Architecture of Catalonia (IAAC).
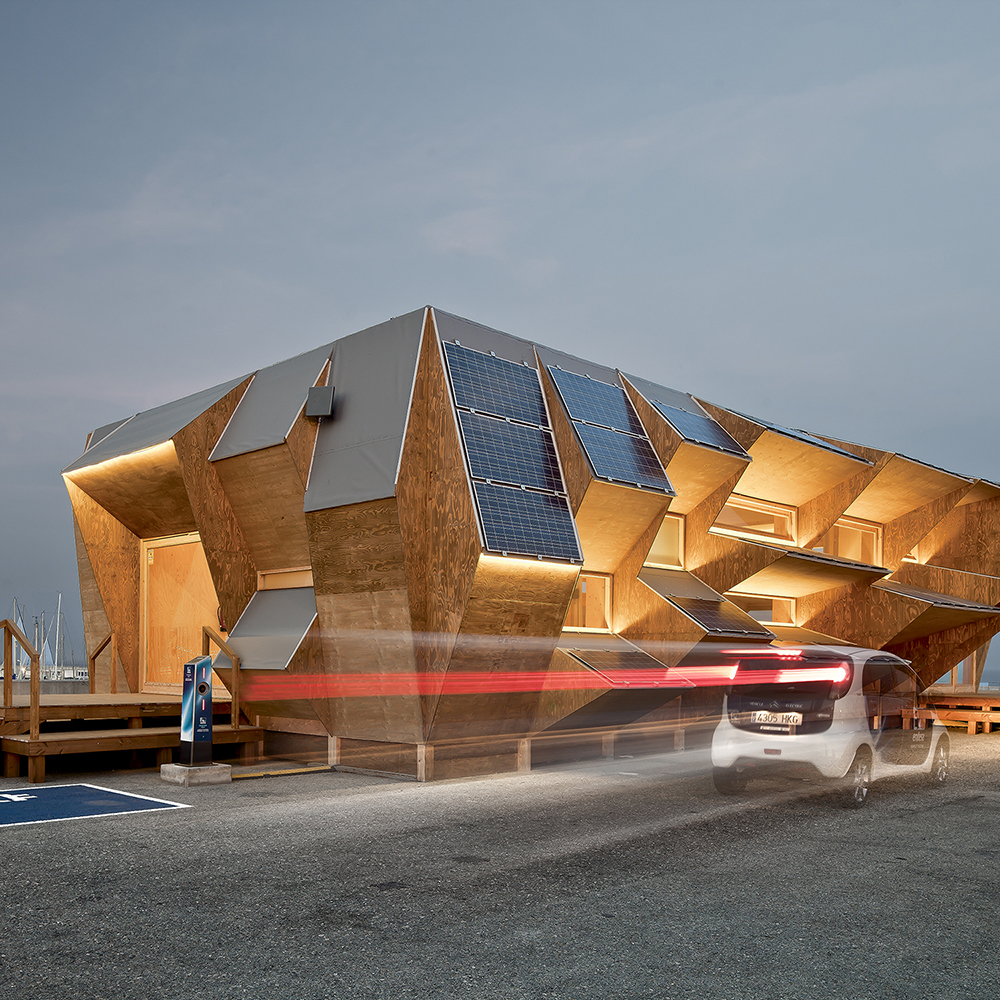
Endesa Pavilion; by Institute for Advance Architecture of Catalonia (IAAC), Spain
ENDESA Pavilion is a self-sufficient solar prototype installed at the Marina Dock, within the framework of the International BCN Smart City Congress. Over a period of one year it will be used as control room for monitoring and testing several projects related to intelligent power management. The pavilion is actually the prototype of a multi-scale construction system. A facade composed by modular components, like solar brick, that respond to photovoltaic gaining, solar protection, insulation, ventilation, lighting. The same parametric logic adapt façade geometries to the specific environmental requirements for each point of the building. It is is a single component that integrates all levels of intelligence that the building needs. From “form follows function” (classic XX century statement) to “form follows energy”. The facade opens reacting to the solar path, being active and becoming permeable towards south, while becoming closed and protective towards north. The behavior of this skin makes visible the environmental and climatic processes that surrounds the prototype.